At Masten, we’ve been developing additively manufactured technologies for rockets and liquid propulsion for more than a decade. Most recently, we teamed up with NASA’s Marshall Space Flight Center in Huntsville and Elementum 3D to take additive manufacturing to the next level. We’re now in Phase II of a Small Business Innovation Research (SBIR) project to pioneer a patent-pending permeable additive manufacturing (PermiAM) process for rocket engines. Backed by NASA’s Space Technology Mission Directorate, PermiAM is one of many space technologies Masten is working on to lower barriers to the Moon, Mars, and beyond.
We’ll dive into what exactly PermiAM is and how it can benefit the industry at large.
What is PermiAM?
PermiAM is Masten’s patent-pending additive manufacturing approach that changes the porosity of metal during the printing process. This method allows us to 3D-print engine components as a single piece using a wider variety of metals, such as aluminum, copper, and Inconel.
In partnership with Elementum 3D, Masten is currently using the PermiAM method to produce transpiration-cooled injector faces that can be used for rocket engines with 7,000 lbf thrust. As rocket fuel passes through them, these injector faces “sweat” on the surface and cool themselves to prevent melting.
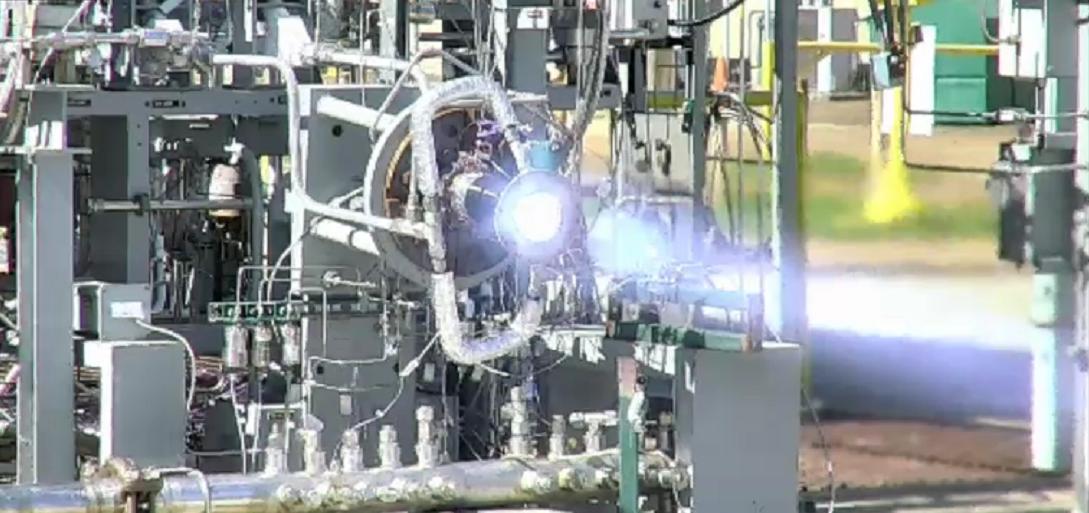
Some of the most commonly used rocket engines in history have used transpiration-cooled injector faces. In most cases, these injectors have been constructed from transpiration mesh that has multiple layers of compressed stainless steel. This technology, which dates back to the Apollo era, uses a lot of welded joints, so the injectors can’t be additively manufactured. They require traditional assembly with 100+ parts, so it’s incredibly labor intensive.
PermiAM addresses this challenge by enabling transpiration-cooled injectors to be additively manufactured as a single piece. The PermiAM process mitigates high temperatures by enabling construction of porous material exactly where cooling is required. As a result, injectors that traditionally required 100+ individual parts can now be 3D-printed as one part with no extra assembly.
What are the advantages?
For starters, PermiAM allows for significant cost and time savings since fewer parts and less labor is required. The results of a trade study for 7,000 lbf thrust engines show traditionally-manufactured transpiration injectors require 12 to 16 weeks manufacturing time and cost $46,000, while PermiAM injectors only require 1 to 2 weeks manufacturing time and cost $19,000. That’s a 60% reduction in manufacturing costs and 92% reduction in manufacturing time.
Other benefits include the ability to lower injector temperatures by thousands of degrees. That means heavy, high-temperature materials such as Inconel are no longer required to prevent melting. Lighter weight materials, such as aluminum, can be used instead to increase payload capacity on spacecraft.
PermiAM also improves the performance and thrust of novel engine designs. It varies the density across the porous injector face to enable strong, lightweight parts that increase engine thrust-to-weight ratio while enabling more engine stability and efficient cooling.
What’s the status?
Masten recently completed three successful PermiAM tests at NASA Marshall. Built in partnership with Elementum 3D, our PermiAM injector was tested on one of NASA’s 7,000 lbf thrust chambers. Three deep throttle tests were performed back to back with excellent engine performance. The final hot fire test ran for 65 seconds with a 380°F measured injector face temperature and a 6100°F combustion temperature. We confirmed there was no face erosion or damage from the 125 seconds of accumulated run time.
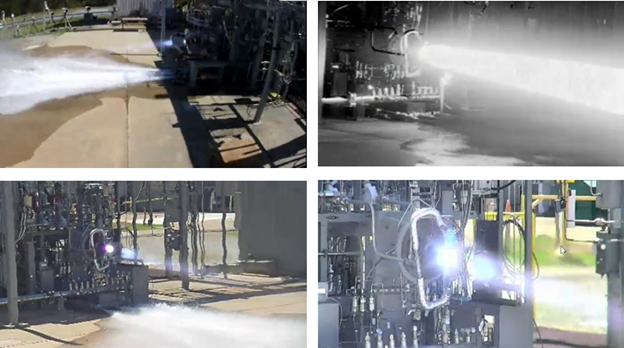
This proves the PermiAM method is feasible and has potential to scale for bigger rocket engines! At Masten, we plan to use PermiAM injectors for future lunar landers and upper-stage engines designed for reusability.
Beyond Masten initiatives, the benefits of PermiAM are industry wide. The PermiAM approach can be used to replace expensive, complex parts that are traditionally manufactured for small satellite launch vehicles, upper-stage engines, and other planetary landers. This approach can help accelerate mission schedules and lower costs to space for both human and robotic missions.