Space Tech
Mission-enabling technologies solving the most pressing challenges in space.
Cutting Edge Technologies
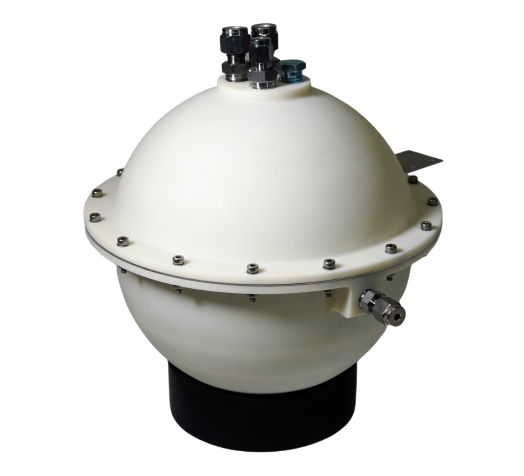
Nite™ System
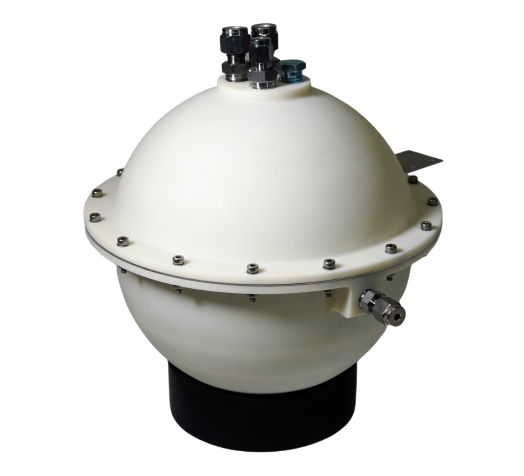
Nite™ System
Rocket Mining System
Rocket Mining System
Lunar PNT Network
Unlike Earth, the Moon isn’t equipped with GPS so lunar spacecraft, assets, and human explorers are essentially operating in the dark. Masten’s new lunar position, navigation, and timing (PNT) solution proposes to fix that with surface-based sensors that can be deployed from a spacecraft into a dedicated sensor array on the Moon. With functionality similar to GPS, the autonomous network can enable navigation and location tracking for spacecraft, assets, and future astronauts on the lunar surface or in lunar orbit.
Lunar PNT Network
Unlike Earth, the Moon isn’t equipped with GPS so lunar spacecraft, assets, and human explorers are essentially operating in the dark. Masten’s new lunar position, navigation, and timing (PNT) solution proposes to fix that with surface-based sensors that can be deployed from a spacecraft into a dedicated sensor array on the Moon. With functionality similar to GPS, the autonomous network can enable navigation and location tracking for spacecraft, assets, and future astronauts on the lunar surface or in lunar orbit.
Fast Landing Pads
Fast Landing Pads
3D-Printed Rocket Injectors
3D-Printed Rocket Injectors
Electric Pumps
We’re also using additive manufacturing techniques to 3D-print high-power electric cryogenic pumps. These pumps can be used in 5,000 lbf engine propulsion systems to provide superior throttling capabilities over traditional turbopumps at significantly lower complexity and cost. Available for methane, oxygen, and hydrogen, they’re lightweight and power dense with the ability to enable propellant transfer and refueling for sample return missions.
Electric Pumps
We’re also using additive manufacturing techniques to 3D-print high-power electric cryogenic pumps. These pumps can be used in 5,000 lbf engine propulsion systems to provide superior throttling capabilities over traditional turbopumps at significantly lower complexity and cost. Available for methane, oxygen, and hydrogen, they’re lightweight and power dense with the ability to enable propellant transfer and refueling for sample return missions.
Deploy Our Tech
Get in touch to learn more about deploying our mission-enabling technologies.